I have told people for years that while I have built with most aircraft construction methods (metal, wood, steel tube/fabric, glas….) and I am an A&P, one skill I never really acquired was welding. Last Christmas (over a year ago) I got a nice welding helmet from Louise, which I took as permission to buy a welder and start learning. With the help of some great mentors, I have been learning to TiG (went through MiG pretty quick, and if I have to weld two tractors together, I can do that….), and after a year, I am proud to say that I am comfortable producing some aircraft parts!
the F1 Rocket has a cockpit crossbar that supports the top of the pilot’s seat, and in teh RV-8, that comes as a single piece. In teh F1, it comes as two side pieces and a raw piece of tubing to cut and weld in place. I have been sweating that job for months, but finally spent much of the last week carefully makign tooling to make th cuts, then practicing the actual welds with scraps of 4130 - and finally welding the final part. Yes I did ground the final welds for appearance, but I am happy with the results - and with a new skill!
Before, with a piece of flat bar standing in for the tube (for measurements)
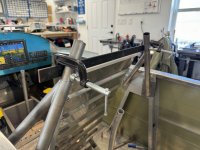
After - with the tube welded in place!
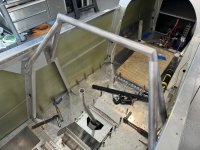
I guess you CAN teach an old dog new tricks - and using eluding in building an RV (like) airplane….
the F1 Rocket has a cockpit crossbar that supports the top of the pilot’s seat, and in teh RV-8, that comes as a single piece. In teh F1, it comes as two side pieces and a raw piece of tubing to cut and weld in place. I have been sweating that job for months, but finally spent much of the last week carefully makign tooling to make th cuts, then practicing the actual welds with scraps of 4130 - and finally welding the final part. Yes I did ground the final welds for appearance, but I am happy with the results - and with a new skill!
Before, with a piece of flat bar standing in for the tube (for measurements)
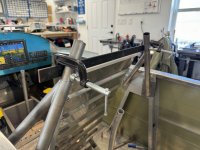
After - with the tube welded in place!
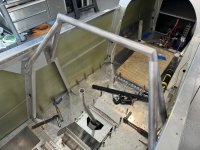
I guess you CAN teach an old dog new tricks - and using eluding in building an RV (like) airplane….