Bill Boyd
Well Known Member
Wife and I started a cross-country to the beach yesterday and we weren’t 15 minutes out when we got an oil temp alarm for 240F. I was in fast cruise-climb and still full rich, with normal CHT’s at the time. I noted the air control knob was sitting slightly back from the full open position. Pushing and holding it in the fully-open position did not alter the trend. I throttled back, trimmed nose down and tried more like 50 fpm but the temp climb continued. When it hit 250F I pulled power and descended to a nearby airport, abandoned on a Sunday morning, and proceeded to pull the upper cowl while things cooled off.
The dipstick read just over 5 quarts, and I normally keep it at 6, so in went the spare quart from the tool kit. No air path obstruction was seen looking down the SCAT and into the cooler mount. I did note the butterfly was cocked a bit from the full open position. Tinkering with the Bowden cable a bit, it looked as if fully open was when the panel knob was about 1/2” out from the panel, so I tried to tape it in that position with electrical tape on the knob shaft. Buttoned things back up and took off, noted Oil T at 170F.
In climb, temp rose slowly as expected and stabilized at about 213-215, which is typical for it. The knob kept creeping out from the panel and I kept shoving it back in to the tape “stop.” Temp would modulate to 220 and back down again each time this happened. We flew the rest of the trip with no issues.
I find it hard to believe that adding a quart of oil made the difference (I always top it at 6qts and add one at 5), and also hard to believe that a slight canting of the butterfly air valve, which was clearly happening, would make the temps exceed redline. In all prior flights and testing, the oil cooler air flow butterfly position has made only about 15 degrees max difference in oil temps - so ineffective that I was considering removing it altogether and possibly just installing a fixed restriction for cold season flying.
Overall, I have been okay with cruise oil temps in the 200-215 range but know they could be better, so I’ve been thinking about adding a bell mouth trumpet to the air intake on the rear baffle over #6. I could also afford to direct some upper cowl airflow away from #4 back to #6 and the oil cooler intake if there is an accepted way to do this. My CHT’s in cruise yesterday were showing #4 about 20F cooler than 2 and 6…
I’m open to suggestions as to cause and cure. I can check the temp sender accuracy in boiling water when I get home in a few days.
Photo is the EFIS in cruise on the second leg after I figured out how to tweak the butterfly for max air flow. #4 is clearly getting more cooling than it needs.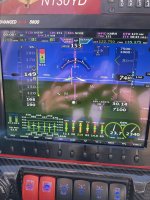
The dipstick read just over 5 quarts, and I normally keep it at 6, so in went the spare quart from the tool kit. No air path obstruction was seen looking down the SCAT and into the cooler mount. I did note the butterfly was cocked a bit from the full open position. Tinkering with the Bowden cable a bit, it looked as if fully open was when the panel knob was about 1/2” out from the panel, so I tried to tape it in that position with electrical tape on the knob shaft. Buttoned things back up and took off, noted Oil T at 170F.
In climb, temp rose slowly as expected and stabilized at about 213-215, which is typical for it. The knob kept creeping out from the panel and I kept shoving it back in to the tape “stop.” Temp would modulate to 220 and back down again each time this happened. We flew the rest of the trip with no issues.
I find it hard to believe that adding a quart of oil made the difference (I always top it at 6qts and add one at 5), and also hard to believe that a slight canting of the butterfly air valve, which was clearly happening, would make the temps exceed redline. In all prior flights and testing, the oil cooler air flow butterfly position has made only about 15 degrees max difference in oil temps - so ineffective that I was considering removing it altogether and possibly just installing a fixed restriction for cold season flying.
Overall, I have been okay with cruise oil temps in the 200-215 range but know they could be better, so I’ve been thinking about adding a bell mouth trumpet to the air intake on the rear baffle over #6. I could also afford to direct some upper cowl airflow away from #4 back to #6 and the oil cooler intake if there is an accepted way to do this. My CHT’s in cruise yesterday were showing #4 about 20F cooler than 2 and 6…
I’m open to suggestions as to cause and cure. I can check the temp sender accuracy in boiling water when I get home in a few days.
Photo is the EFIS in cruise on the second leg after I figured out how to tweak the butterfly for max air flow. #4 is clearly getting more cooling than it needs.
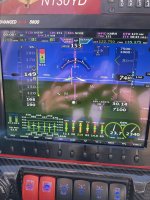
Last edited: