What Lycoming Key Reprints has to say about boost pump
Here is a snap shot of where I got the info and the permission to reprint.
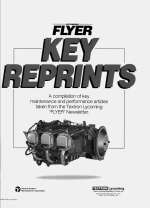
The following is a Copy / Paste from the above 12.1 MB PDF document.
Use Of Fuel Boost Pumps With Textron Lycoming Engines
As an engine manufacturer, we are frequently asked
about the proper use of the fuel boost pump with our
powerplants. Although we can't pretend to be an expert on
the fuel boost pump itself, we have some positive
recommendations concerning its use with our engines.
Where a boost pump is provided by the airframe
manufacturer, and the airframe Pilot's Operating Handbook
has a limited treatment of the use of the fuel boost pump,
perhaps this discussion can provide the necessary fuel boost
pump information for the pilot in order to operate his or her
engine as safely as possible.
It is necessary to supply the engine with a steady,
uninterrupted flow of fuel for all operating conditions.
Entrapped air, temperature changes, pressure drops,
agitation in the fuel lines and other factors affect the release
of air and vapor from the fuel system. Under some
circumstances where an engine mounted fuel pump is
provided it may not be able to pump a continuous fuel
supply free of excessive vapor.
An effective continuous fuel supply is provided by use
of the fuel boost pump. As a general recommendation, the
fuel boost pump should be used with Lycoming engines in
all conditions where there is any possibility of excessive
vapor formation, or when a temporary cessation of fuel flow
would introduce undesirable hazards. The conditions under
which Textron Lycoming recommends operation of the fuel
boost pump are as follows:
1. Every takeoff.
2. Climb after takeoff unless Pilot's Operating Handbook
says it is not necessary.
3. When switching fuel selectors from one separate fuel tank to another, the fuel boost pump should be "On" in the new tank until the operator is assured there will be no interruption of the fuel flow.
4. Every landing approach.
5. Any time the fuel pressure is fluctuating and the engine is affected by the fluctuation.
6. Hot weather, hot engine ground operation where fuel vapor problems cause erratic engine operation
7. Some General Aviation aircraft require the use of the fuel boost pump during high-altitude flight. This will be spelled out in the Pilot's Operating Handbook.
8. If the engine mounted fuel pump fails.
If the fuel boost pump is used during ground operation,
don't fail to check the condition of the engine mounted fuel
pump before takeoff by turning the boost pump off briefly,
and then back "on" for takeoff. If the engine mounted pump
has failed, it would be safer to know that on the ground
rather than in the air when the fuel boost pump is turned
"off."
When in doubt, do the safest thing and use the fuel boost
pump with Lycoming engines. Don't be "stingy" with the
boost pump. In most cases they last the overhaul life of the
engine, and are then exchanged or overhauled themselves.
AS A REMINDER, the airframe Pilot's Operating
Handbook is the authority if boost pump information is
spelled out in it.
Following is a photo image of the page as well as a PDF of the page.
View attachment KEY REPRINTS (dragged).pdf