I have run some turbocharger operating point calculations using the Garrett "Boost Advisor" predictive tool. Basically trying to understand what happens to the turbo operating point from sea level to 15k ft. The first thing I did was to put together a table of atmospheric conditions from sea level to 30k ft. This would be absolute pressure and temperature in 2500ft increments. I was able to use the temperature data in the "Boost Advisor".
The thing that baffles me regarding the results is that the tool suggests that to make the SAME hp at increasing altitude requires progressively higher mass flow with altitude. Higher air flow means higher fuel flow which should equate to more power ? What am I missing ? This seems to violate some law of physics.
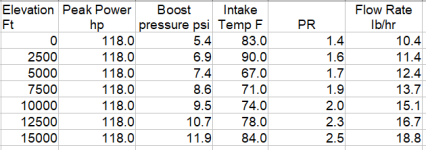
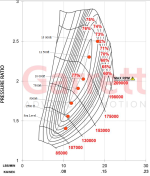
The thing that baffles me regarding the results is that the tool suggests that to make the SAME hp at increasing altitude requires progressively higher mass flow with altitude. Higher air flow means higher fuel flow which should equate to more power ? What am I missing ? This seems to violate some law of physics.
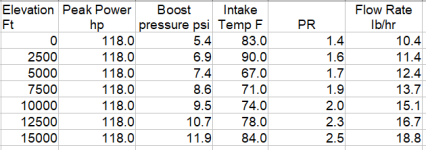
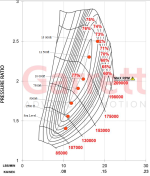